The Book of Metal
“Make sure it is hard and lasts a long time!”


The Bolting Bible
This is free resource by HowNOT2 and our way of contributing to the community. It's nice to understand what you are clipping and trusting with your life, even if you never plan on installing or removing bolts. We also believe that if you are going to spend time and money to bolt something, you should do it well.
This book is in a blog format. This page points to all 17 chapters, and the end of each chapter points to the next.
A downloadable PDF is available HERE.
Think Long Term
Just like mom always said, “it’s what’s on the inside that counts!” What your bolt is made out of really matters if you want it to last a long time. Most of the bolts you see on the shelf at the local hardware store are not going to make it more than a few seasons. And you can’t just buy whatever you want on any bolt-specific online retailer, even if they market directly to climbers. Some sell zinc plated hardware without being very very clear it should only be used for indoor gyms or very, very, very dry deserts.Zinc

So the next level of protection is to use chemicals and electricity to apply a very thin metal coating to protect it. Zinc can corrode up to 100x slower than other metals but is much weaker than steel, so steel is often “zinc-plated”. Fun fact - zinc isn’t a hard metal, in fact it is less than half as hard as steel (159DPM hardness vs 70DPM hardness). The zinc is a “sacrificial coating”, so when it is plated on steel, it will always tarnish and corrode first. However it is very thin, and naturally doesn’t give long term protection in any environment with moisture. Once it has fully corroded, the steel underneath begins to rust. Plated steel is generally intended for interior uses.

To make steel last longer, more zinc can be added. However, that takes a completely different process called galvanization. Hot-dipped galvanized coatings is a 7 step process creating a metallurgical bond and can achieve a bond of 3,600 psi (harder than the base steel). This creates the rough surface you see on galvanized nails, but since the threads on galvanized screws can’t be too rough, it is spun in a centrifuge to clear the threads of excess zinc, though it still requires an oversized galvanized nut.
Think of cooking a piece of chicken in a pan with a little oil in the bottom (zinc plating) vs deep frying that turkey (galvanizing). They both have oil on it, but one has a much thicker coating. Zinc-plated products are not intended to be an outdoor building material, but galvanized is, however, it doesn’t last forever and is not an ideal outdoor anchor. As soon as the zinc is gone, the steel underneath corrodes quickly.

EPISODE: Galvanized eye bolts don't corrode quickly but stainless steel does???
Plated steel bolts can last 20 years in most areas before they need to be replaced. However, in as little as 3 months in areas like Thailand, Brazil or Hawaii they can be broken off by hand due to the corrosive nature of water, salt, heat and the chemicals in the rock. Interestingly enough, there is enough zinc coating on the galvanized eye bolts used on the coast of Portugal that they are lasting 20 years, which is impressive near the ocean.

Stainless

The word “stainless” is thrown around like it is a specific type of steel, when in fact there are 5 types or categories with a total of 150 grades. Chromium and nickel are the 2 major ingredients to make steel more resistant to corrosion (not corrosion-proof). They don’t plate steel with these metals, they melt them together creating an alloy. The two different grades you will see in climbing bolts are 304 and 316 stainless. 304 Stainless Steel is also referred to as 18/8 (18% chromium, 8% nickel). Most stainless climbing bolts and hangers are made out of 304 grade and are significantly more resistant than any plated steel but fail quickly when near the ocean.

316 stainless or “marine-grade” is better because they throw just a little Moly in the recipe. 18% Chromium & 10% Nickel & 2% Molybdenum, and less than 1% of carbon, phosphorus, sulfur, nitrogen. The Molybdenum is added to help resist corrosion to chlorides (salts) like in coastal areas. 316SS is the most corrosion resistant mechanical bolt that you can buy since titanium isn’t available as a mechanical bolt (only as glue ins).
However, in the harsh conditions of Thailand, Brazil and Hawaii, 316 stainless climbing bolts can completely fail within 3 years and so something even more corrosion resistant is required. We played with these discontinued 400 stainless hangers in this EPISODE.
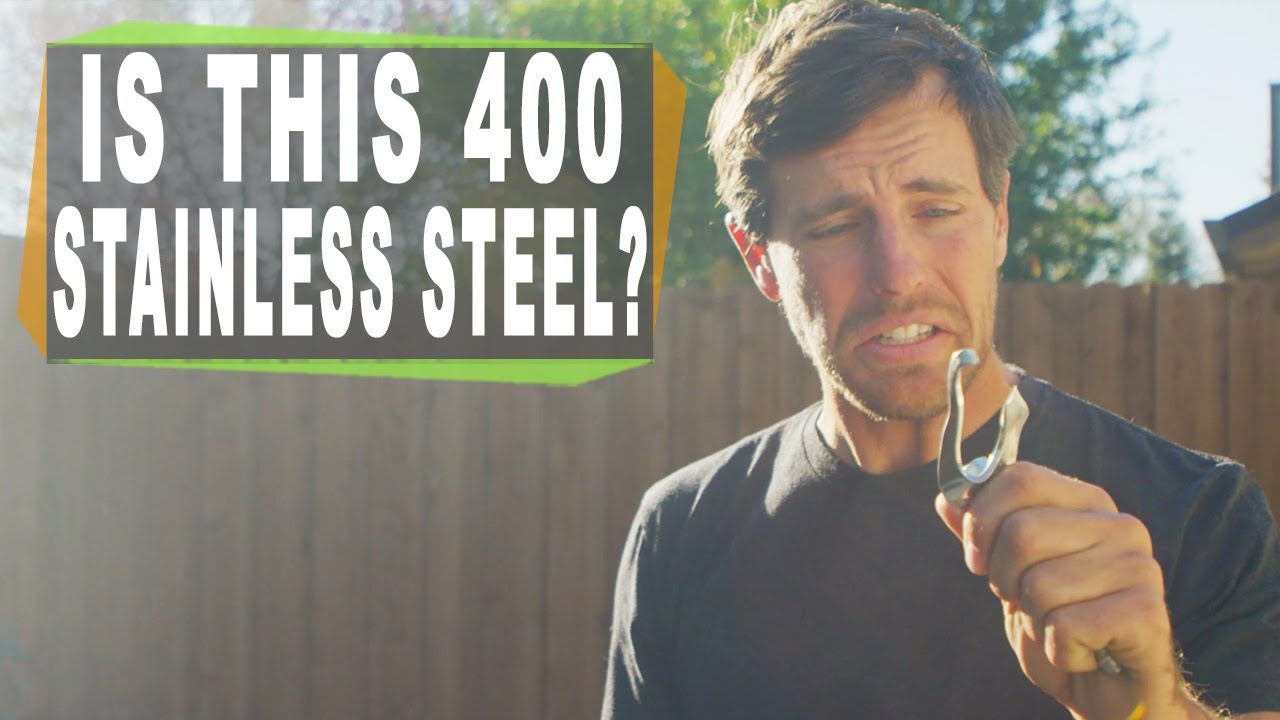

However, Peter Randelzhofer put out a paper testing Fixe’s anchor PLX chain links that were in an outdoor covered climbing gym in the Netherlands and they discovered cracks near the welds. Apparently duplex steel 1.4362 is easier to weld but duplex steel 1.4462 is better for corrosion. So the chains they tested were 5kn under the 25kn mbs in only 2 years in mild outdoor conditions.

Fun fact: INOX is sometimes stamped into bolts. It is a french way of saying stainless from the word “inoxydable”. It could be 304 or 316 SS but it doesn’t mean duplex stainless, that has PLX stamped into it.
Titanium

Fun fact: titanium is the 9th most abundant element on earth and melts at 3,135F (400F more than steel). Titan Climbing manufactured the first certified titanium glue in bolt. It’s a “P” shape made from one continuous rod so there is no structural weld point to break. It requires a 14mm, or ⅝ inch hole and has an MBS of 35kn.

They are about 30% more expensive than marine grade stainless and similarly priced to Bolt-Products duplex SS, but are much more corrosion resistant.
Durability
Sometimes, corrosion isn’t the #1 concern but wear and tear. Jim Titt from www.bolt-products.com demonstrated in an experiment that titanium wears down about twice as fast as stainless does. He buried these metal links in a box with dry, sandy soil and had a 10mm rope run back and forth 1.6m or 5 feet through the two different metals and got these results.- 0 cycles - SS 8mm, Titanium 8mm
- 100 cycles - SS 7.52mm, Titanium 7.07mm
- 200 cycles - SS 6.76mm, Titanium 5.74mm
- 300 cycles - SS 6.07mm, Titanium 4.37mm
- 400 cycles - SS 5.53mm, Titanium 3.57mm
- Titanium (left photo) wears about twice as fast as SS (right photo)


Rust

Galvanic Corrosion

Climbing Magazine published an article saying that as long as the bolt isn’t near the ocean or constant water, galvanic corrosion isn’t that bad. They may be right in the fact some rust doesn’t mean it’s a death trap…. today. However, eventually it will rust enough to be dangerous and you don’t know when that is. If you spend a couple extra dollars, you can install something that won’t rust at all.
Stainless on titanium in theory can have galvanic corrosion but not in the real world use that we use our hardware. So a stainless pigtail/ramshorn can be placed on a titanium glue in, however if you needed a titanium bolt due to the elements, then chances are you need all the hardware to be titanium, so again, you wouldn’t mix the metals.




Stress Corrosion Cracking
We love the coast, but the coast doesn’t love our bolts. So many coastal areas, especially in Thailand or Malta, eat away stainless bolts quickly, even 316SS. Fixe calls their 316SS “marine grade” but it is not suitable for all marine environments. Other factors that speed up corrosion can be elevated temperatures, crevices, mixed metals, mixture of high and low humidity, overhanging rock where rain cannot rinse off harmful chemicals and compounds. See the bolts failures in these photos and see how important titanium glue in bolts are in corrosive environments. This ARTICLE gets in the weeds and This VIDEO is also gnarly!







David Reeve's has found that 304SS it's not just susceptible to the chlorine induced "stress crack corrosion" but also sulphide stress cracking coming from BACTERIA??? For an in-depth dive into how limestone by the seashore eats 304 stainless check out his awesome work at Crag Chemistry

Getting Nerdy About 304SS
Crag Chemsitry has a very nerdy ARTICLE about 304 and why it's not always super good enough. It's a rather complex subject.Just a glimpse… Dave research indicates that 304 fails because: (1) it has a high transformation temperature meaning that (2) when being transformed into a bolt at room temperature it gets a high content of austenite converted to martensite. (3) Martensite is permeable to atomic hydrogen. (4) Hydrogen causes embritlement of all stainless alloys. (5) In some sea shore limestone crags there are high levels of sulphates. (6) Sulphate reducing bacteria feed out of them and poop compounds that react with the metal and release atomic hydrogen into it. (7) The atomic hydrogen embritles the alloy, creating cracks and cavities. (8) Bacteria colonize the cracks and start getting deep into the metal. (9) The process repeats.
316 seems to do better because: (1) it has a lower transformation temperature meaning that (2) when cold-formed at room temperature it won't develop that much martensite.
Staining
Just like skid marks on your underwear, we should avoid the same problem on our rocks. When the zinc coating on plated steel is exposed to hydrogen and oxygen (aka water) long enough it creates zinc hydroxide (similar to iron oxide which is rust). Zinc hydroxide is a white powder that forms and can leave streaks on the rock. Also when the iron is exposed, it will rust, not only making the bolt dangerous but leaving the areas looking… shitty.




Camouflage

PAINT - Roughing up the metal with sandpaper and spraying them with Rustoleum at home prior to installation is one way but that process doesn’t last forever if the bolt is exposed to elements or used often. You can increase the adhesion by priming it first and doing several THIN layers. Etching zinc plated hangers, is obviously bad, as the zinc coating is super thin and when your paint wears off, you have unprotected steel exposed.



Stainless isn’t stoked for some etching either. Jim Titt from Bolt-Products.com explains the risk in painting stainless in this forum. “Stainless steel gains its corrosion resistance by producing chromium oxide which is passive and prevents further surface corrosion by blocking oxygen diffusion to the steel surface, this blocks corrosion from spreading into the metal's internal structure. Passivation occurs only if the proportion of chromium is high enough and oxygen is present, a coating which prevents oxygen reaching the surface prevents passivation from happening. The usual problem is that the coating either becomes damaged (by tightening the bolt or by karabiners) or porous due to aging and allows water to penetrate which becomes anaerobic. We passivate all our products during manufacture and any attempt to apply a surface coating using methods such as abrading or etch priming is removing the passive layer.”
Powder Coat - As a painting contractor, I can attest to the fact that powder coated surfaces definitely last longer than painted surfaces, but it isn’t permanent by any means. Metolius sells their Enviro stainless hangers in dark grey and tan and Fixe has 4 colors - black, grey, tan and rust, each in ⅜” or ½” holes. These come in 304 stainless which is awesome but they sell them also in plated steel.


Alternative Coatings Automotive paint can be a fancy and expensive way to camo. And Plasma coatings are next level in overkill if you really are determined to hide your bolts while having chaulk tick marks on the route! I doubt plasma will be available from your climbing bolt suppliers anytime soon when people try to save pennies per hanger when establishing routes.

Conclusions
1) Never use zinc plated bolts. Some places are dangerous to use and in other places it can last 20 years before needing to be replaced. If you are 20 years old, that might sound like. along time, but it's not. Let's think long term so people in 100 years aren't climbing routes that look like swiss cheese.2) Don’t mix metals or you risk bimetallic corrosion, speeding up the corrosion of 1 of the components of your bolt.
3) Coastal areas cause excessive exposure to corrosion that even 316SS or even PLX HCR stainless may not withstand and so titanium might be your only option. If it is a lower-off anchor and will have ropes running through it constantly, stainless will hold up twice as long as titanium as long as the environment is suitable for it. Don’t be cheap with people’s lives, so please install the highest quality bolts if people are going to trust their life to them.


What's Next?

Chapter #5 - The Book of Hangers